Safenet2
Description
The DECOVALEX Task SAFENET is dedicated to better understand fracture nucleation and evolution processes in crystalline rocks, with applications in nuclear waste management, but also in geothermal reservoir engineering. Further improvement of fracture mechanics models is required for both applications, specifically (i) improvement of numerical methods for fracture mechanics under THMC conditions and based on this (ii) providing applied tools for performance and safety assessment for nuclear waste management as well as for reservoir optimisation for geothermal applications. As a continuation of SAFENET with a previous focus on benchmarking fracture models and experimental laboratory analyses (see D2023 Task G references below), SAFENET-2 is dedicated to model extension and validation from laboratory to field scale.
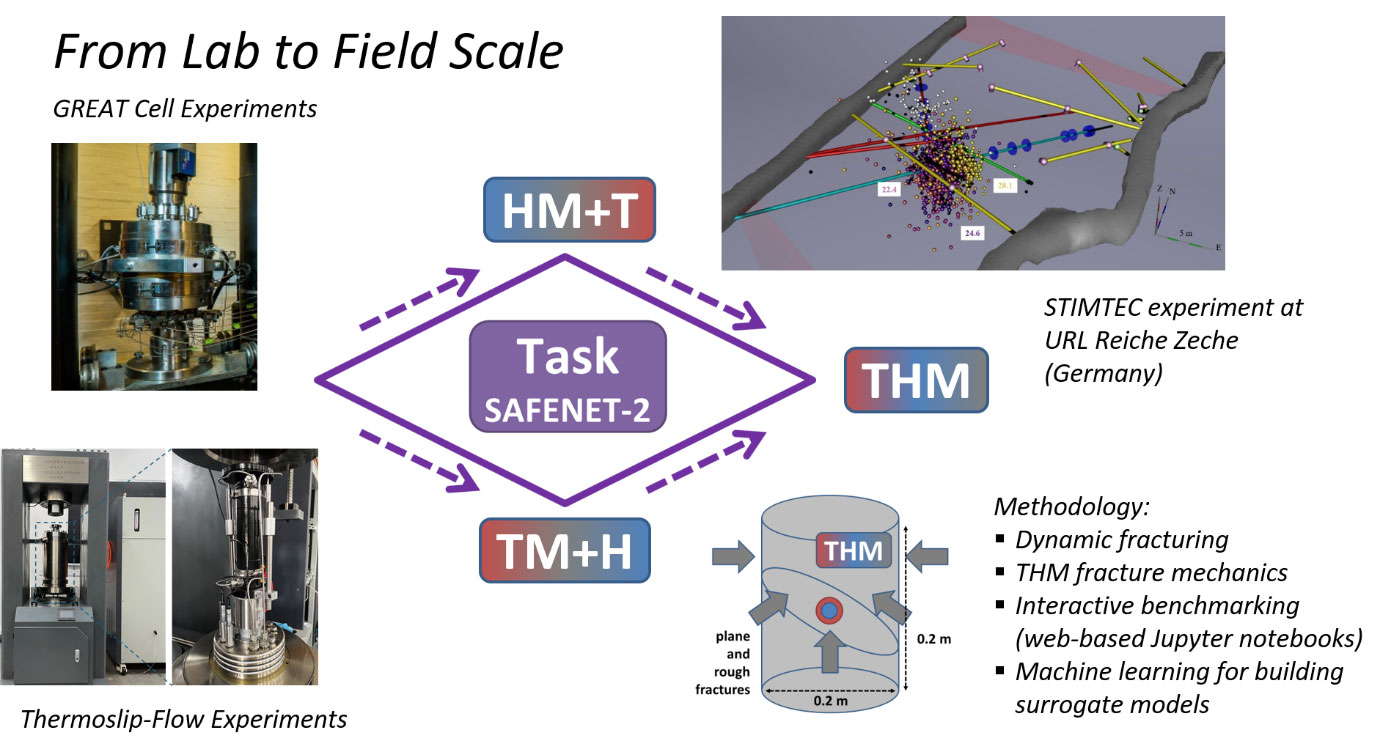
Experimental Data
The experimental data basis consists of laboratory and field scale experiments.
2.1 GREAT cell large laboratory scale data
The GREAT cell provides the capability to create hydraulic fractures in rock samples under a controlled triaxial stress field, and to change that stress field during the experiment enabling the investigation of the impact of normal and shear stress on fracture permeability. The sample size is 200 mm diameter x 200 mm height, and strain is measured along the middle circumference of the cylinder. Strain is recorded using a fibre optic cable attached to the surface of the sample, enabling a high spatial (every 2mm) and temporal (100 Hz) resolution of strain to be recorded, and the deformation during the process of fracturing to be recorded.
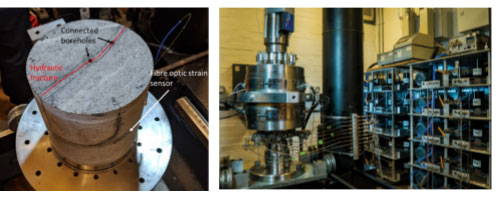
2.2 Thermoslip-flow lab scale data
Using the customized fault shear flow testing machine at Chongqing University, an inclined natural rock rough fracture cutting through a cylindrical rock specimen (50 mm diameter x 100 m length) is initially loaded close to criticality (σ1 and σ3). The specimen is then heated by the concentrated heat source (embedded heater in the lower part of the specimen) to induce thermal stress increments in the principal stress. Fluid is injected through the fluid inlet (bottom) and flows through the fracture to the fluid outlet. The pressure at the inlet and outlet is monitored. Fracture slip is then thermally induced. The fluid flow characteristics before and after thermally induced fracture slip are analysed. In this way the THM coupled behaviour of a rock fracture is studied.
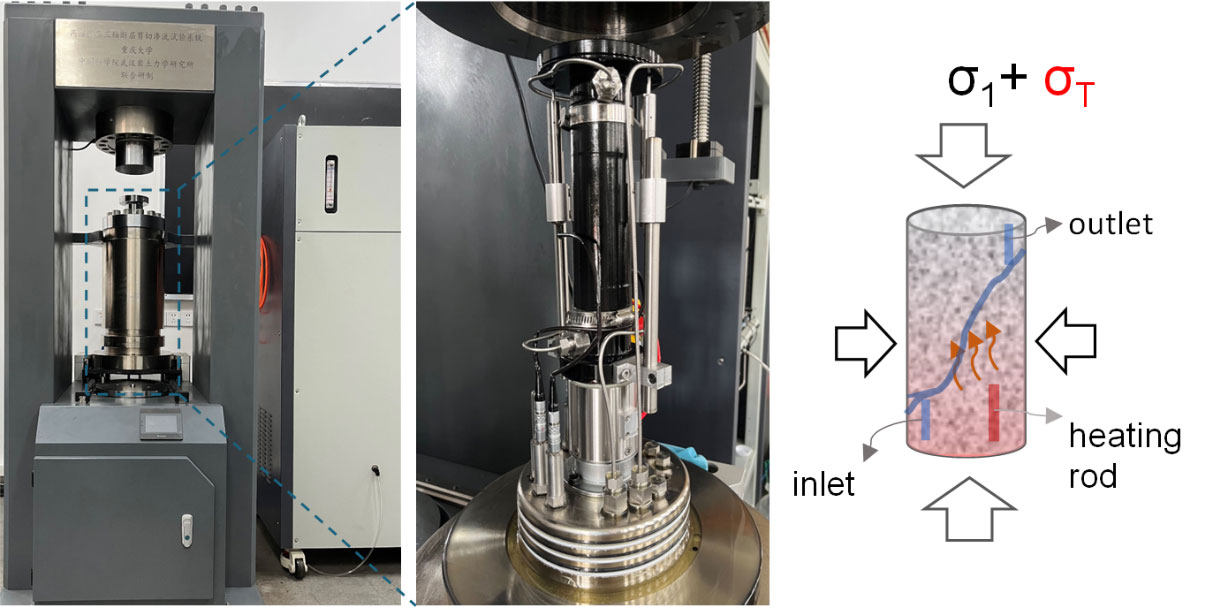
2.3 STIMTEC in-situ experiment data
The experimental basis at field scale is provided by the STIMTEC experiment in the URL Reiche Zeche where stimulation tests with periodic pumping tests and high-resolution seismic monitoring have been conducted (Boese et al. 2021, 2022, 2023). Together with the laboratory experimental data, the STIMTEC experiment will provide a basis for upscaling fracture models from laboratory to field scale concerning hydro-mechanically induced fracture processes.
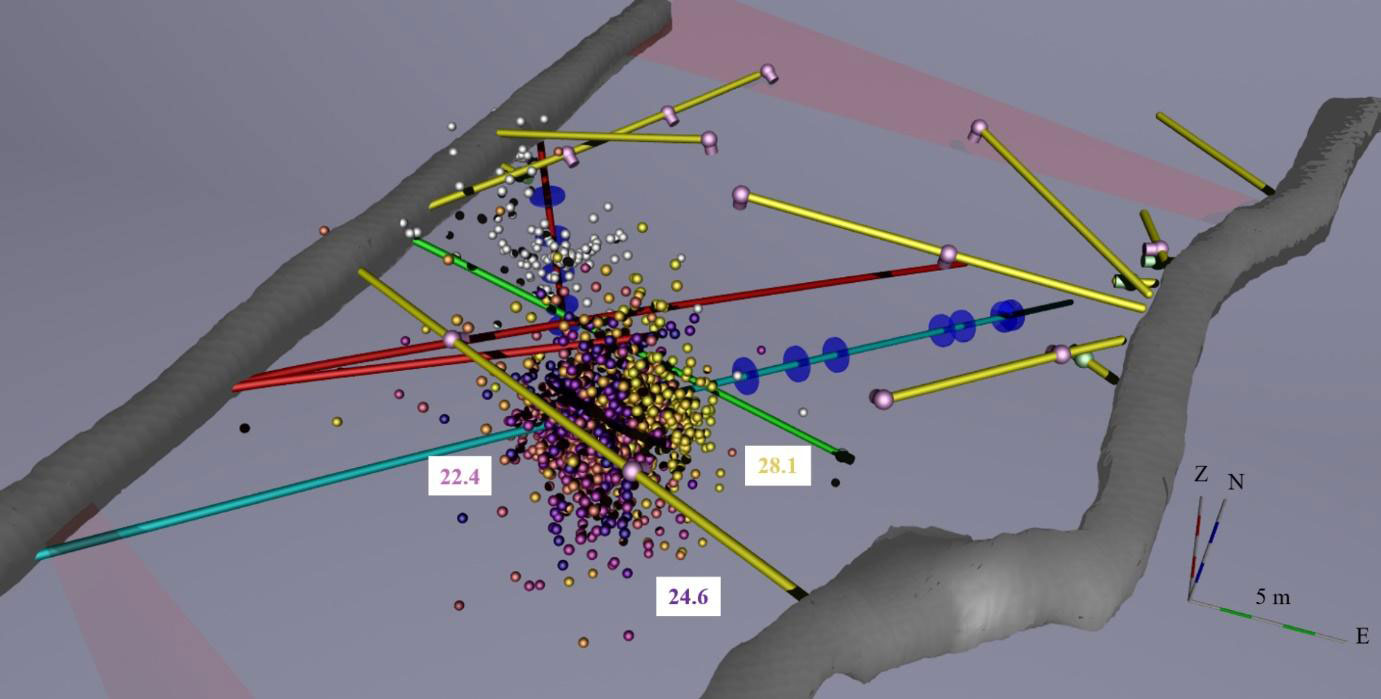
Approach
The task is divided into two groups (i) conceptual work (Steps 0 and 4) and (ii) experimental analyses on lab and field scales (Steps 1-3)
Step 0: Benchmark simulation
Providing a benchmark suite for GREAT cell and Fracture thermoslip-flow laboratory experiments addressing the experimental main features by simplified and conceptual models. The benchmark suite will be provided as open science contribution via interactive Jupyter notebooks.
Step 1: GREAT cell test case simulation
Three experiments conducted with Gneiss and Granite samples are available for simulation.
A “large” natural heterogeneous foliated Freiberg Gneiss Sample is hydraulically fractured under axial load confined conditions, and unconfined radial conditions – the fracture is free to form according to the influence of foliations:
- Process Dynamic Fracture Formation, unconfined
- Material: Freiberg Gneiss
- Conditions : σ1 = 8 MPa, σ2 = σ3 = 0, Ø = 200 mm
- Experimental Data : Time dependent fluid pressure, surface deformation @100Hz, dynamic fracture growth recorded
Two “large” Granite Sample are hydraulically fractured under axial load confined conditions, and confined radial conditions. Two boreholes are drilled into the fracture to facilitate fluid flow measurements, and estimates of permeability under different stress and fluid flow conditions are available:
- Process Dynamic Fracture Formation, confined x2
- Material: Granite
- Conditions : σ1 = 24 MPa, σ2 = σ3 = 8 MPa, Ø=200mm
- Conditions : σ1 = 32 MPa, σ2 = σ3 = 12 MPa, Ø=200mm
- Experimental Data : Time dependent fluid pressure, surface deformation @100Hz, dynamic fracture growth recorded.
Step 2: Thermoslip-flow test case simulation
Step 2 test case simulation will commence in late 2025. More information will be available and distributed to the research team during 2nd workshop in October 2024, and 3rd workshop in May 2025.
Step 3: STIMTEC in-situ experiments
Hydraulic injection and stimulation results will be analysed in order to characterize in-situ fracture permeabilities. Acoustic emission data will be used for constraining fracture mechanics models.
Step 4: Synthesis and open sciences
Results will be synthesized for evaluation of numerical methods, model upscaling from laboratory to field scale, and applicability of the methodology for related application areas (e.g. geothermal reservoirs in crystalline rock). SAFENET-2 will actively contribute to open science action, e.g. by providing benchmarking tools via an interactive web platform.
Participating Groups
- UFZ/RUB (Ruhr University Bochum), BGR, TUBAF
- Chinese Academy of Sciences
- DOE – LBNL (Lawrence Berkeley National Laboratory)
- DOE – SNL (Sandia National Laboratory)
- Edinburgh University
- DynaFrax/CQU (Chongqing University)
- KIGAM
- Taiwan Power Company (TPC)
Further Information
For further information, please contact the task leaders, Olaf Kolditz, Chris McDermott, and Jeoung Seok Yoon.
References
SAFENET
- Kolditz O, CI McDermott, JS Yoon, Mostafa Mollaali, Wenqing Wang, Mengsu Hu, Tsubasa Sasaki, Jonny Rutqvist, Jens Birkholzer, Jung-Wook Park, Chan-Hee Park, Hejuan Liu, Peng–Zhi Pan, Thomas Nagel, Son Nguyen, Saeha Kwon, Changsoo Lee, Kwang-Il Kim, Alex Bond, Teklu Hadgu, Yifeng Wang, Li Zhuang, Keita Yoshioka, Gonçalo Benitez Cunha, Andrew Fraser-Harris (2024): DECOVALEX Task G Synthesis Paper: A systematic model- and experimental approach to hydro-mechanical and thermo-mechanical fracture processes in crystalline rocks (submitted to Geomechanics for Energy and the Environment - GETE)
- Kolditz O, McDermott C, Yoon JS, Zhuang L, Renner J (2024): SAFENET-2: Safety ImplicAtions of Fluid Flow, Shear, Thermal and Reaction Processes within Crystalline Rock Fracture NETworks. Task introduction, DECOVALEX 2027, 1. Workshop, 02.05.2024 (online)
- Mollaali, M., Kolditz, O., Hu, M., Park, C.-H., Park, J.-W., McDermott, C.I., Chittenden, N., Bond, A., Yoon, J.S., Zhou, J., Pan, P.-Z., Liu, H., Hou, W., Lei, H., Zhang, L., Nagel, T., Barsch, M., Wang, W., Nguyen, S., Kwon, S., Lee, C., Yoshioka, K. (2023): Comparative verification of hydro-mechanical fracture behavior: Task G of international research project DECOVALEX–2023. Int. J. Rock Mech. Min. Sci. 170 , art. 105530 10.1016/j.ijrmms.2023.105530
GREAT cell
- A.P. Fraser-Harris, C. I. McDermott, G. D. Couples, K. Edlmann, A. Lightbody, A. Cartwright-Taylor, J. E. Kendrick, F. Brondolo, M. Fazio, and M. Sauter (2020), Experimental Investigation of Hydraulic Fracturing and Stress Sensitivity of Fracture Permeability under changing Polyaxial Stress Conditions, Journal of Geophysical Research, Solid earth, 2020-12, Vol.125 (12).
- C. I. McDermott, A. Fraser-Harris, M. Sauter, G. D. Couples, K. Edlmann, O. Kolditz, A. Lightbody, J. Somerville, W. Wang, 2018, "e;New Experimental Equipment Recreating Geo-Reservoir Conditions in Large, Fractured, Porous Samples to Investigate Coupled Thermal, Hydraulic and Polyaxial Stress Processes."e; Scientific Reports 8(1): 14549.
STIMTEC
- C.M. Boese, Kwiatek, G., Dresen, G., Fischer, T., Renner, J. (2021): AE-type hydrophone performance during the STIMTEC and STIMTEC-X hydraulic stimulation campaigns at Reiche Zeche Mine, Germany. 55th U.S. Rock Mechanics / Geomechanics Symposium 2021, 4
- C.M. Boese, Kwiatek, G., Fischer, T., Plenkers, K., Starke, J., Blümle, F., Janssen, C., Dresen, G. (2022): Seismic monitoring of the STIMTEC hydraulic stimulation experiment in anisotropic metamorphic gneiss. Solid Earth, 13 (2), pp. 323-346.
- C.M. Boese, Grzegorz Kwiatek, Katrin Plenkers, et al. (2023). “Performance Evaluation of AE Sensors Installed Like Hydrophones in Adaptive Monitoring Networks During a Decametre-Scale Hydraulic Stimulation Experiment”. In: Rock Mechanics and Rock Engineering 56.10, pp. 6983–7001. doi: 10.1007/s00603-023-03418-9.